mig welding wire speed and voltage chart pdf
Summary
Download the ultimate MIG welding wire speed and voltage chart PDF. Optimize your welds with precise settings for flawless results!
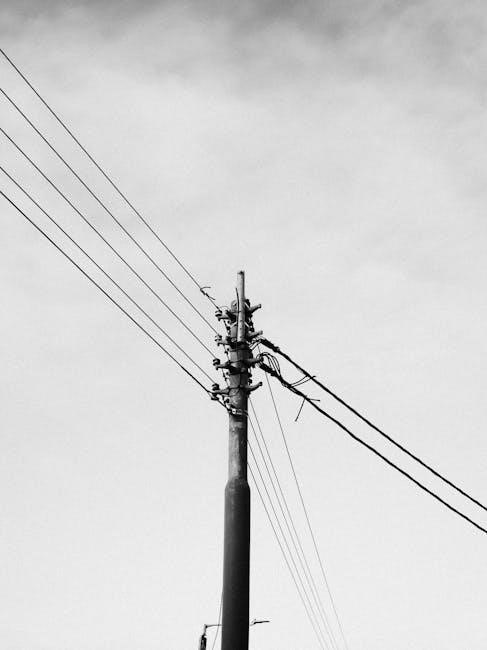
MIG welding wire speed and voltage charts provide essential guidelines for optimal welding settings. These charts help establish the ideal balance between wire feed speed and voltage, ensuring consistent weld quality across various materials and thicknesses. By referencing these charts, welders can quickly determine the appropriate parameters for their specific projects, minimizing trial and error. They are indispensable tools for achieving precise control over the welding process.
1.1 Importance of Wire Speed and Voltage in MIG Welding
Wire speed and voltage are critical parameters in MIG welding, directly influencing weld quality, penetration, and bead appearance. Wire feed speed determines the current, affecting heat input and fusion. Voltage controls arc length and stability, ensuring proper metal transfer. Incorrect settings can lead to poor penetration, lack of fusion, or excessive spatter. Consistent wire speed and voltage ensure uniform welds, making them essential for achieving desired mechanical properties. Proper adjustment prevents defects and enhances efficiency, making these settings fundamental for successful MIG welding operations across various materials and thicknesses.
1.2 Purpose of Using a Wire Speed and Voltage Chart
A wire speed and voltage chart serves as a practical guide to establish optimal welding parameters. It provides precise settings for different materials, thicknesses, and joint types, ensuring consistent weld quality. By referencing the chart, welders can quickly determine the ideal wire feed speed and voltage, reducing trial and error. This tool is essential for achieving proper penetration, avoiding defects, and maintaining mechanical properties. It also helps in selecting the right settings for various shielding gases, enhancing efficiency and reliability in MIG welding processes across industrial applications.
Factors Affecting MIG Welding Settings
Material thickness, wire diameter, joint type, and shielding gas significantly influence MIG welding settings. These factors determine optimal voltage and wire speed for consistent weld quality.
2.1 Wire Diameter and Its Impact on Welding Parameters
Wire diameter plays a crucial role in MIG welding, affecting both voltage and wire feed speed. Thicker wires, such as 0.030″, require higher voltage and faster feed speeds to maintain a stable arc, while thinner wires, like 0.023″, need lower settings to prevent overheating. The appropriate wire diameter ensures proper penetration and bead formation, making it essential to consult charts for specific material and thickness combinations to achieve optimal welding results.
2.2 Material Thickness and Joint Type
Material thickness and joint type significantly influence MIG welding parameters. Thicker materials require higher voltage and wire feed speeds to achieve full penetration, while thinner materials need lower settings to prevent burn-through. Joint type, such as butt or fillet welds, also affects the required arc characteristics. For example, fillet welds may demand slightly lower voltage to control bead size and shape. Consulting charts ensures optimal settings for specific combinations of material thickness and joint geometry, promoting consistent and high-quality welds. Adjustments may vary based on the desired weld penetration and appearance.
2.3 Shielding Gas and Its Influence on Arc Characteristics
Shielding gas composition and flow rate significantly impact MIG welding arc characteristics; Common gases include Argon, Helium, and CO2 mixtures, each affecting arc stability, penetration, and weld cleanliness. Argon provides a smooth, stable arc, while Helium increases voltage and heat input. CO2-rich mixes enhance penetration but may increase spatter. Proper gas selection ensures optimal arc performance, reducing porosity and improving weld quality. Higher gas flow rates stabilize the arc, while lower flows risk contamination. Consulting charts helps match gas type and flow to material and joint requirements, ensuring consistent welding results and minimizing defects.
Understanding Wire Feed Speed (WFS)
Wire Feed Speed (WFS) is crucial in MIG welding, determining the rate at which the electrode wire is fed into the weld pool. Proper WFS ensures consistent arc stability, avoiding issues like porosity or lack of fusion. Higher WFS increases deposition rates but may reduce penetration, while lower speeds enhance precision but limit productivity. Adjusting WFS according to material thickness and joint type is essential for achieving desired weld quality and appearance. Charts provide specific WFS ranges for different wire diameters and materials, guiding welders to optimal settings efficiently.
3.1 Relationship Between Wire Feed Speed and Voltage
The relationship between wire feed speed (WFS) and voltage is critical in MIG welding. As WFS increases, higher voltage is typically required to maintain a stable arc. This balance ensures proper arc characteristics, such as consistent heat input and weld penetration. Charts often illustrate this relationship, showing how voltage adjustments correspond to changes in WFS for different materials and thicknesses. Maintaining this balance is key to achieving high-quality welds without defects like undercutting or lack of fusion. Proper setup enhances both productivity and weld integrity.
3.2 How to Set the Wire Feed Speed for Different Materials
Setting the wire feed speed (WFS) for different materials requires careful consideration of factors like thickness and type. Thicker materials generally need higher WFS to maintain penetration, while thinner materials require lower settings to prevent burn-through; Referencing a WFS chart helps determine the optimal range for specific materials, such as steel, aluminum, or stainless steel. Adjustments may also be needed based on joint type and desired weld appearance. Proper setup ensures consistent weld quality and minimizes rework, making the process more efficient and reliable for various applications.
Voltage Settings in MIG Welding
Voltage settings in MIG welding control the arc’s heat and shape, impacting weld penetration and bead appearance. Proper voltage ensures a stable arc and quality welds consistently across various materials and thicknesses, optimizing the welding process for desired outcomes.
4.1 Arc Voltage and Its Effect on Weld Penetration
Arc voltage directly influences weld penetration and bead formation. Higher voltage increases heat input, enhancing penetration depth but potentially causing excessive melt-through on thinner materials. Lower voltage reduces penetration, suitable for thinner materials or surface-focused welds. Maintaining the optimal voltage ensures the desired weld profile without compromising material integrity or aesthetics. Proper voltage adjustment, guided by charts, is crucial for achieving consistent and high-quality welds in various applications.
4.2 Adjusting Voltage for Optimal Weld Quality
Adjusting voltage is critical for achieving optimal weld quality. Too high a voltage can lead to over-penetration and burn-through, while too low may result in lack of fusion. By referring to voltage charts, welders can fine-tune settings to match material thickness and desired weld characteristics. Proper voltage adjustment ensures uniform bead formation, adequate penetration, and minimal distortion. Regular monitoring and precise control of voltage are essential for maintaining consistent weld quality across various projects and materials.
MIG Welding Wire Speed and Voltage Chart
This section provides a detailed chart outlining wire speed and voltage settings for various materials and thicknesses, ensuring accurate welder setup for optimal results.
5.1 Typical Wire Speed and Voltage Ranges for Common Materials
For carbon steel (0.6mm wire), typical wire speeds range from 180-400 IPM, with voltages between 14-19V. Stainless steel (0.8mm wire) often uses 150-350 IPM and 15-20V. Aluminum (0.9mm wire) may require 200-450 IPM and 16-22V. These ranges ensure proper fusion and penetration, varying slightly based on material thickness and joint type. Always consult the chart for precise settings to achieve consistent weld quality and avoid defects.
5.2 Example Chart for Different Wire Diameters and Thicknesses
Below is an example chart illustrating typical wire speed and voltage settings for various wire diameters and material thicknesses:
Wire Diameter | Material Thickness | Wire Speed (IPM) | Voltage (V) |
---|---|---|---|
0.6mm | 1/8″ | 200-300 | 16-18 |
0;8mm | 1/4″ | 150-250 | 18-20 |
0.9mm | 3/8″ | 250-350 | 20-22 |
This chart provides a quick reference for setting up your MIG welder based on material thickness and wire size, ensuring optimal weld quality and penetration.
Practical Applications of the Chart
The chart serves as a practical guide for setting up MIG welders, troubleshooting issues, and optimizing weld quality. It helps welders quickly reference ideal parameters for specific materials and thicknesses, ensuring efficient and precise welding operations.
6.1 Setting Up Your MIG Welder for Specific Welding Tasks
Using the wire speed and voltage chart, select the appropriate wire diameter and material type. Refer to the chart for recommended voltage and wire feed speed based on material thickness and joint type. Adjust the welder settings accordingly, ensuring proper shielding gas flow. Test the weld on a scrap piece to verify penetration and bead appearance. Fine-tune settings if necessary to achieve the desired results, ensuring consistent weld quality and efficiency.
6.2 Troubleshooting Common Welding Issues Using the Chart
When encountering issues like inconsistent weld penetration or porosity, consult the wire speed and voltage chart to identify potential misalignments. If the weld is too shallow, increase voltage slightly. For excessive spatter, reduce wire speed. Porosity may indicate insufficient shielding gas or incorrect voltage settings. Adjustments should be made incrementally, testing each change. Referencing the chart helps pinpoint deviations from optimal parameters, guiding corrections to achieve desired weld quality and minimize defects efficiently.
Safety Considerations
Ensure proper equipment setup to prevent electrical hazards and use personal protective equipment (PPE) for eye and skin protection. Always follow safety guidelines to avoid accidents.
7.1 Proper Equipment Setup to Avoid Electrical Hazards
Proper equipment setup is crucial to prevent electrical hazards in MIG welding. Ensure the welder is placed on a stable, dry surface and connected to a grounded power source. Always use the correct cable sizes and ensure all connections are secure. Regularly inspect the welding gun, cables, and power source for damage. Follow the manufacturer’s guidelines for equipment setup and maintenance. Proper setup ensures safe operation and minimizes the risk of electrical shocks or fires, promoting a safe working environment for welders.
7.2 Personal Protective Equipment (PPE) for MIG Welding
Personal protective equipment is essential for safeguarding against hazards in MIG welding. A welding helmet with a shaded lens protects eyes from UV/IR radiation and sparks. Fire-resistant gloves prevent hand burns, while a welding jacket or apron shields clothing from heat and spatter. Steel-toe boots and nonflammable pants further enhance safety. Proper ventilation ensures inhalation of fumes is minimized. Always inspect PPE before use to ensure it is in good condition. Adhering to PPE guidelines significantly reduces the risk of injury during welding operations.
MIG welding wire speed and voltage charts are essential tools for achieving optimal weld quality. They guide welders in setting the right parameters, ensuring consistency and efficiency in every task.
8.1 Summary of Key Points
Key points emphasize understanding wire speed and voltage relationships, material thickness, and shielding gas effects. Proper setup using charts ensures optimal weld quality, avoiding common issues. Consistent settings yield better results, and safety measures are crucial.
8.2 Final Tips for Achieving Consistent Weld Quality
Use wire speed and voltage charts as a starting point, then fine-tune settings for specific materials. Maintain consistent wire feed and voltage to avoid porosity or lack of penetration. Cleanliness of the workpiece is crucial. Always wear proper PPE and ensure good ventilation. Regularly inspect and maintain welding equipment. Practice technique and refer to manufacturer guidelines for optimal results. Adjustments should be incremental to achieve desired weld characteristics.